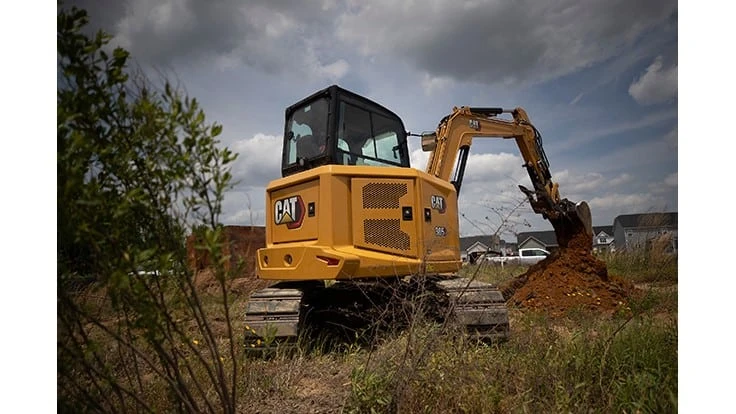
Caterpillar is debuting the new 4-tonne, Cat 304, and 5-tonne, Cat 305 CR, Next Generation Mini Hydraulic Excavators, which deliver more power to the pumps, higher bucket breakout forces and deeper standard digging depths to increase performance by up to 20% over their E2 series counterparts. Their grease intervals and extended filter service life, combined with common components throughout the line and flat, easy-to-replace side panels, deliver up to 10% lower owner and operating costs.
The new 304 and 305 CR models are the final machines to be reengineered to the Cat next generation mini hydraulic excavator line concept. From the 1.5- to 10-tonne class models, all 17 – 20 Cat mini hydraulic excavators in the range (depending on region) offer common features and consistent controls layout to simplify training and operator adaptation.
Built with a new reduced radius design, the 304 features a narrow, 1700-mm (66.9-in) track width, 254 mm (10 in) slimmer than the 304 E2, for more versatility and access to confined spaces. While narrower, the new 304 design increases performance, balance and stability of the 4-tonne class model. Its reduced radius allows for greater stability, both 360-degree and when traveling with loads, while its extra counterweight option takes the model to a higher level of stability.
The new engine on the 5-tonne class Cat 305 CR Excavator delivers nearly 9% greater power to increase machine performance. Hydraulic system improvements provide higher breakout forces – 49.2 kN (11,061 lbf) bucket, 28.3 kN (6,362 lbf) standard stick and 25.2 kN (5,665 lbf) long stick – to improve digging efficiency in hard rock applications. It also offers 140 mm (5.6 in) deeper dig depths than the 305 E2, giving it more application flexibility. Its compact radius swing reduces overhang when working to the side, while its 1980-mm (78-in) track width and new extra counterweight option help to optimize stability and lift performance in confined spaces.
Both excavator models now offer an angle dozer blade option to optimize machine flexibility in backfilling and finish grading applications. In addition to offering ample above- and below-grade travel with standard float function for easy clean-up, the angle blade moves 45 degrees left or right of center. Increasing efficiencies and reducing operator interaction with final grading, angle blade movement is controlled by the right-hand joystick, while the left joystick handles machine drive.
Tailoring machine weight to job requirements, interchangeable counterweight packages offer the balance between low ground pressure and lifting performance. Their industry-exclusive Cat Stick Steer System simplifies machine control by allowing the operator to switch from conventional lever/foot-pedal steering controls to low-effort joystick operation. Two travel speed ranges and standard cruise control facilitate moving around the jobsite with minimum operator interaction.
Meeting U.S. EPA Tier 4 Final and EU Stage V emission standards, the turbocharged Cat C1.7 Turbo engine delivers higher power than the previous C2.4 engine. Standard auto idle, auto engine shutdown and efficient load-sensing hydraulics with variable displacement pump help to lower fuel usage at the site for more affordable operation. High main-relief pressures, coupled with flow rates, generates the hydraulic capacity for high digging and lifting forces and more efficient use of a range of attachments. Complete with quick-disconnect lines, the standard auxiliary system provides the choice of one-way, two-way or continuous flow.
Common to most Cat next generation mini hydraulic excavators, the sealed and pressurized cab enclosure is available with heating and/or air conditioning for all-weather climate control. The cab’s large glass areas plus skylight afford all-around visibility. The large display with advanced touchscreen option provides intuitive machine function control and easy monitoring of critical operating parameters. A canopy option is available in some regions.
Daily maintenance checks for the 304 and 305 CR are quickly made from ground level through side doors. Expanded use of common parts throughout the line plus their damage-resistant exterior construction help to reduce parts inventory investment and lower repair costs. Increased service intervals mean these excavators spend more time on the job and less time in the shop.
Offerings may vary by region, for more information on the new Cat 304 and 305 CR Mini Hydraulic Excavators can be found here.
Additionally, Caterpillar now offers Cat Grade technologies as an aftermarket option to owners of Cat next generation mini hydraulic excavators in the 6- to 10-ton class range. Available through Cat and Sitech dealers, owners can equip the excavators with Cat Grade with Advanced 2D or Cat Grade with 3D. The field kit’s modular components facilitate quick installation, while the technology seamlessly integrates into the Cat next generation excavator electronics infrastructure.
Both aftermarket grade technologies mirror the capabilities of larger Cat excavators operating Cat Grade with Advanced 2D or 3D systems, allowing the equipment to reach target grade quickly. A separate, 254-mm (10-in) high-resolution touchscreen monitor allows operators to conveniently view, create and work site designs inside the cab. Automatics deliver simple, single-joystick control over the stick and bucket to maintain grade and avoid overcutting and undercutting.
Cat Grade with Advanced 2D uses on-board processors and fast-response sensors to deliver real-time bucket tip and elevation guidance on the touchscreen monitor. This technology gives operators the ability to create and work to basic site designs, while grade design edits can easily be made from the operator’s seat. Field installation of the technology includes the hardware, sensors and dedicated monitor for grade plan creation, editing and viewing.
Using GPS and GLONASS systems to pinpoint the excavator’s exact location, Cat Grade with 3D allows multiple machines to grade to complex jobsite designs. The monitor shows bucket position throughout the full range of the digging motion, while height and depth audio alerts indicate when desired grade has been reached to protect from overcutting or undercutting. Beyond the hardware and sensors, including monitor, required for Grade with Advanced 2D, installation of Grade with 3D also requires GNSS receivers and antennas.
Beneficial in a range of applications including sewer and septic work, digging footings and flat pad home development, Cat Grade technologies help operators reduce the number of passes and shortens the time it takes to complete cuts. They improve grade quality and consistency for operators of all experience levels and can extend the workday by aiding work in limited visibility situations. Saving costs associated with time, labor, fuel and material consumption, Cat Grade technologies allow companies to reach target grade quickly and lower overall operating costs at the jobsite.
More information on Cat Grade with Advanced 2D and Cat Grade with 3D for Cat 6- to 10-ton class mini hydraulic excavators can be found here.
Latest from Lawn & Landscape
- All fun and games
- Larry Ryan steps down as Ryan Lawn & Tree president
- Session snippets
- WorkWave debuts WavelyticsTM at Beyond Service User Conference
- Picking up after the storm
- HD Hyundai Construction Equipment North America unveils HX90A compact excavator
- Ruppert Landscape acquires Ocean Woods Landscaping
- Registration now open for Central Coast Water Summit