In the field, landscape contractors have a wide variety of pruning equipment at their fingertips, everything from hand-held tools that trim delicate branches to heavy-duty, gas-powered chainsaws that easily slice through thick tree limbs.
Each tool performs a specific function in arbor care, and thoroughly understanding those roles helps contractors increase job site effectiveness, efficiency and – when it comes to the gas-powered cutting tools – overall safety.
According to recent Lawn & Landscape research, nearly 55 percent of landscape contractors offer tree and ornamental trimming and removal services. And of those contractors providing the services, 17 percent indicated their revenues from arbor and tree care services increased from 2005 to 2006. With more contractors offering these services to boost revenue, it is imperative to have the right tools to do the job correctly. However, a mistake many contractors make is confusing cutting and pruning products designed for homeowner use with those products intended for professionals, says Rod Buff, owner of Buff Landscaping in Libertyville, Ill. The consistent use of some landscape tools, such as saws and pruners, requires contractors to invest in professional-grade equipment, Buff says. “A homeowner would edge their grass about once a week whereas a landscape contractor would be getting 10 times more use out of the same piece of equipment in a day,” he says.
A cutting tool made for the average homeowner is not going to have the same durability as a product made for arbor care professionals, Buff says. Contractor-grade cutting equipment is going to stand up to the rigors of daily use, he says, whereas lesser-grade tools lack dependability.
When purchasing professional-grade cutting and pruning tools there are specific quality features contractors will benefit from, says Anita Gambill, a representative for Stihl in Virginia Beach, Va. “Contractors should look for hand tools that have rust resistant blades that can be sharpened and eventually replaced, a quick release blade lock and a comfortable non-slip grip,” she says. Corroded cutting equipment will not work correctly and contractors will end up replacing tools more often if they are not rust resistant, she adds.
MAN POWER. Hand-held pruning shears are the smallest of the cutting tools available and are beneficial when tending to small-sized plant material. There are two types of pruning shears contractors use in the field. Anvil pruners squeeze the branch between a blade and a flat cutting surface and use pressure to snap the branch. Bypass pruners, though, scissor the branch between two sharp blades for a cleaner cut. Both are handy for removing easily accessible branches at the ground level, especially hedges and ornamental bushes. They cut through limbs up to 3/4 of an inch in diameter. A quality pair of professional-grade pruning shears will cost a contractor between $10 and $50.
“Pruning shears are useful for ornamental pruning like Japanese maples and Dogwoods,” says Erich Schneider, CEO and founder of Schneider Tree Care in Greenville, S.C.
The lopper is the pruning shear’s bigger cousin. This hand-held cutting tool provides more control and power over the cut because the user is able to grip the tool with both hands.
“The lopper can be thought of as a long two-handed pruning shear,” says Rob Fanno, owner of Fanno Saw Works in Chico, Calif. “It has a bigger hook and blade so it can cut through thicker branches.”
Gripping a lopper with both hands allows the user to tap into his or her upper-body strength to cut branches between 1 and 2 inches in diameter. Contractors normally use loppers to cut thicker and harder branches, such as those on rose bushes and fruit trees. It also provides contractors with a reach capability for limbs that don’t require a ladder but are beyond a worker’s reach. On average, a professional-grade pair of loppers costs between $35 and $85.
If hand-held shears and loppers don’t make the cut, a contractor should upgrade to saws. There are two types of hand saws: folding and non-folding. The folding saw blades range between 6 and 18 inches whereas the non-folding saw blades range between 8 and 26 inches. The folding saw’s smaller blade size and folding capability makes it more convenient for contractors to move them from job site to job site.
When choosing between the conventional saw tooth and the Japanese-style teeth, many contractors prefer the Japanese style, Fanno says. The Japanese style blade provides more slicing action making it easier for users to quickly cut through hard woody material. Hand saws cut limbs between 1 to 12 inches in diameter and, on average, cost between $15 and $40.
Pole saws, on the other hand, allow a contractor to keep both feet on the ground while making cuts to a tree’s canopy. A pole saw resembles a hand saw but with a longer handle that can cut limbs between 1 to 8 inches in diameter. However, workers can also use a pole saw to reach outer limbs while in the tree, Schneider says. Besides trimming a tree’s outer branches for aesthetic purposes, these saws are used to trim back branches from utility poles.
These extension saws cost between $15 and $70. Pole saw handles come in lengths anywhere from 2 to 16 feet and are made from either wood or fiberglass. Handles are available with additional sections to increase a saw’s length.
ENGINE POWER. Every morning, Sam Hill, owner of Sam Hill Tree Care, Dallas, Texas, arms each employee with a hand pruner, hand saw, pole saw and small chainsaw so they can begin another full day of pruning and tree removal.
The chainsaw, however, is the bread and butter of Hill’s tree pruning business. Valuable time and business would be lost without them, Hill says, which is why he keeps a couple of older, but functional, units to put into service when the others breakdown.
Chainsaws have been available to landscape contractors for some time. The first chainsaws used a scratcher chain which ripped its way though wood but did not pull the chips out, says Andy Kuczmar, senior director of product training and support, Echo, Lake Zurich, Ill. In 1946-47 the chain was refashioned in the form of the letter C and the front was sharpened to have a knife-like edge. This new chain works in two parts. The first part severs the grain and the second part acts as a chisel and pulls the chip out. This invention cut down on the amount of time it took to cut a piece of wood.
That chainsaw weighed 70 to 80 pounds and needed two people to operate it. “What changed the industry was not the chainsaw itself,” Kuczmar says. “What revolutionized the whole industry was the design of a new chain that would actually cut,” he says.
Over the years chainsaws have become smaller, lighter and more contractor-friendly. “There were noticeable improvements made in vibration reduction throughout the 1980s and 90s while in recent years the industry has seen continual improvements in cleaner, more fuel-efficient two-stroke engines,” says Andy Stanush, product manager of chainsaws and power cutters, Husqvarna, Charlotte, N.C.
Even the materials chainsaws are made from have changed. Before, the body of the chainsaw was made from aluminum, but today manufacturers use engineering nylons. “There are three advantages to using nylon,” Kuczmar says. “Nylon will absorb vibrations. Nylon will not corrode. Nylon is lighter.” These advancements have made it easier to carry and use chainsaws when working up in trees.
Chainsaws are ideal for extensive cutting and pruning. “Tree care professionals prefer lightweight and high-performance tools due to the amount of time they spend using the saw while in the tree or in bucket trucks,” Stanush says.
Chainsaw costs vary depending on a unit’s size, weight and bar length. The average cost for a small but high-performance professional chainsaw ranges between $400 and $500, Stanush says. The top-handle chainsaw and the rear-handle chainsaw are two types of saws recommended for landscape contractors performing tree trimming services. Logically, the top handle has its controls – the pull throttle, primer and the choke button – on top of the chainsaw while the controls for the rear handle are located on the rear of the unit. Their uses, though, differ. A top-handle saw, for example, is used for tree trimming by those in buckets or on rope, whereas a rear-handle chainsaw gives the operator more control because the controls are spaced further apart. “For a beginner I strongly suggest the rear-handle saw because it provides more control and stability,” Kuczmar says. “The top-handle saw is for those who know what they are doing.”
Along with size and weight, contractors should consider chainsaw features such as air filtration systems, easy access to fuel and oil filters, adjustable chain tension, automatic oilers and vibration reduction systems.
Some contractors choose to use their chainsaws until they die while others dispose of their old ones to upgrade to newer products. Sometimes it is easier to buy a new chainsaw than it is to repair a 6-year-old machine, some contractors say. For example, with an older machine a contractor will wait longer for repair parts compared to modern parts.
“Chainsaws will last as long as you are willing to repair them,” Buff says.
Sponsored Content
A Secret Weapon for Growing Your Lawn Care Business
Retargeting ads allow you to re-engage visitors who leave your lawn care website without converting, helping you stay top-of-mind and increase leads. This article explains how retargeting works, why it’s effective, and how to implement it for your business.
Complete Online Marketing SolutionsKeeping tools clean also extends their lives. For example, Hill’s crews begin each day cleaning and servicing their tree-cutting equipment. Before leaving the yard, air filters are checked and chainsaws are cleaned with compressed air.
Chainsaws need to be oiled and air filters changed regularly. Continued use of a dirty filter is detrimental to the machine. Buff makes sure there are plenty of extras around so dirty ones are replaced right away.
A mistake many contractors make when purchasing a chainsaw is not knowing how to properly select one. “Select a size that will take care of approximately 75 percent of your needs,” Kuczmar suggests. Contractors should also shop for the right weight, balance and power. Contractors should not purchase on bar length alone.
Most contractors believe the longer the bar length the more work they will get done. What they should be thinking is engine size and the horsepower they are going to get from the chainsaw, meaning the more work they will complete, Kuczmar says. If contractors only consider bar lengths they will end up with a heavy tool that creates more friction and cuts slower due to the excessive length of the bar.
Finally, contractors should consider the type of equipment dealer they want to buy their chainsaws from and their experience in working with arbor care professionals. “Do they have the replacement parts, and is the company available when you need them?” Fanno says.
Buff was looking for a reliable company with quality products and a fast turn around time when it came to acquiring replacement parts. “I was willing to pay more to get a good product because I didn’t want to lose labor,” he says.
Hill cautions against going places other than a professional equipment dealer to purchase chainsaws and other cutting tools. For him it’s a service issue. “You buy enough tools from a dealer they start to know you,” he says. “They have all your records of purchases, repairs and warranties in their system. The benefit of going to a dealership is they can direct you to the right tool for your needs.”
Quality cutting tools, however, are only as good as the worker using them. Equipping ill-prepared workers is a common contractor mistake, Fanno says. As soon as an untrained employee picks up a tool they become a liability, he says.
Contractors say it is not uncommon to see unprepared workers holding chainsaws one-handed and lifting them above their shoulders. “It is very dangerous because the lightness of the chainsaw gives them a false sense of security,” Hill says.
Providing employee training can help reduce the amount of on-site accidents. Buff’s various crews have weekly meetings on safety and afterward employees must fill out a report on what was discussed, who was there, and any suggestion they might have. They also have meetings to introduce new products and, if an accident has occurred, they meet to talk about it.
Get curated news on YOUR industry.
Enter your email to receive our newsletters.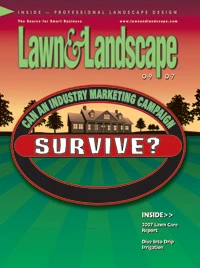
Explore the September 2007 Issue
Check out more from this issue and find your next story to read.