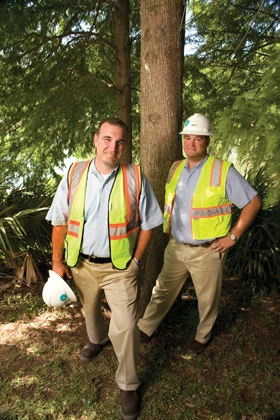
Benton Foret sat down at a table in a conference room in Houma, La., just south of New Orleans. He’d just been given a job he wasn’t sure he could handle. This is big. But his second thought was: How are we going to do this? He told BP he’d think about it, and started dialing. To pull off a project of this scope in such a short time frame, he would need a construction company, about 50 carpenters and a host of other contractors. He wasn’t sure he could do it. But everyone he called told him the same thing: Don’t tell them no. We’re not going to let you fail. Damn the torpedoes. Let’s get this done. “I kind of had a moment there, and it was an uplifting time,” Foret says. “That was at the point where the momentum began to change. We’re going to do this. This is going to happen.” In short order, Foret sat down with the facilities manager, the general contractors and an architect, who drew up the plans for the trailer installation – called “Trailer City” – on the spot. “That’s what served us well through that crisis. People put their egos on the side to work together as a team. Tired? Yeah. Every day, we were tired. Stressed? Yeah, every day. But you know, you lift each other up in those times of doubt,” Foret says. Managing the people. Stressed is a bit of an understatement. By the time Foret and his crews were working full-force to help BP, the spill had been going on for a month. Media and government pressure to solve the problem ratcheted up every day. Add hundreds of people working 14-hour shifts in 90-degree heat – in jobs they aren’t used to doing – and you’ve got the potential for some problems. “It was kind of an understanding without saying it that we’re all in this together. Whether I’m the guy supplying the diesel fuel for all the generators or the guy actually putting up silt fence, we all do it with a sense of urgency. Everybody just worked together wonderfully,” Foret says. At its peak, 175 people were working on the trailer project. His company also built out parking lots, ran water lines, installed hundreds of feet of fencing and constructed an entire decontamination facility. To staff the operations, Foret pulled from his full-time mowing crews, hired college students home for the summer and sought out subcontractors from a variety of trades to finish each project “You see what’s unfolding and the sense of urgency and the adrenaline kind of keeps you going,” he says. “It was definitely an environment that a landscaper would not be accustomed to. It’s not something we did every day.” Handing over the reins. Sponsored Content Lawn and Landscape Marketing on a BudgetDigital marketing can feel overwhelming when you’re working with a limited budget. Websites, SEO, social media, and paid ads can quickly add up, but you don’t need to do everything to see results. By focusing on cost-effective strategies, you can still make a big impact without overspending. Spring in Louisiana is hot. Plants grow fast and the Foret brothers still had a host of landscape clients who, while not responding to a massive oil spill, still needed to be taken care of. But as the response work ramped up, it quickly became clear that they wouldn’t be able to run their two landscape companies and handle the needs of BP at the same time. So, the brothers thought, how could they handle this emergency situation – and tremendous opportunity – without alienating their long-time clients? They delegated, and handed the day-to-day reins of Foret Land & Tree to Operations Manager Ben Hillman. He’d been with the company about a year at that point, working as a crew foreman. “It was a little challenging. I was still getting used to the language barrier … that was kind of trying at times,” says Hillman, who recently left the company to return to his career in oil field sales. “It was pretty well common sense, so I just kind of did what I thought was best. I did what I had to do.” Foret is clear when asked about the importance of this decision: “Clearly he took on the challenge and stepped up. Had it not been for him, we would not have been able to do it,” Foret says. A year later. This summer, Foret and his crews are working to hand over management of their projects to BP. They aren’t doing as much construction work this year – it’s little more than half the company’s business now, and Foret plans on winding it down even further. His focus is a pending move into a newly renovated location. But, a year later, Foret says he’s learned a lot from the spill – about his company, and himself. “In a business like we run in the landscape industry, the construction industry, time spent planning is the most valuable time you can spend in anything you do. “You cannot execute, you cannot just show up to work every day, without having spent some really good quality time in planning and scenario evaluation – if A happens, what’s going to happen as a result?” Foret says. “We could not have done the volume of work in the time period in which we did it without having been brought into the culture that BP followed as far as planning.” And despite the long hours, the stress and pressure, Foret still sometimes can’t believe he and his company pulled it off. “I still sit here and think to myself,” he says. “Did that really happen?” The author is editor of Lawn & Landscape. He can be reached at cbowen@gie.net. |
Get curated news on YOUR industry.
Enter your email to receive our newsletters.
Explore the June 2011 Issue
Check out more from this issue and find your next story to read.
Latest from Lawn & Landscape
- Sgro named Yanmar Compact Equipment's North American president
- Aphix acquires Curb Appeal Landscaping in Birmingham
- Project EverGreen helps revitalize Milan Park in Detroit
- Trex Company wins Product of the Year, Judges’ Choice Winner at Environment+Energy Leader Awards
- General Equipment & Supplies in Fargo adds Takeuchi equipment
- Mariani Premier Group acquires Hazeltine Nurseries
- EnP Investments adds Mark McCarel as Northeast territory sales manager
- Our April issue is now live