For Jason Reale, vice president and owner of Castlewood Custom Landscape & Design in Littleton, Colo., there is no doubt which hand tool is the most essential – a tape measure.
“The quickest way to lose money in the field is inaccurate measurement during estimation and bidding,” he says. “If the actual size of a project is bigger than what was indicated in the plan, you are behind before you even start.”
Perhaps reflecting his bachelor’s degree in computer science from the University of Colorado, Reale also includes the construction laser level as essential. “They give you a superior level of accuracy,” he says. “They are more convenient and save time. For measuring and setting grades, a laser level cuts the time in half compared to pulling strings.” Reale also says that Castlewood could not do without demo saws. “Especially for cutting natural stone, we have to have a heavy-duty, gas-powered saw,” he says. “We always have a back-up because renting one in our area today is $800 a week.”
Whether Castlewood crews are moving rocks, digging trenches, planting trees or spreading mulch, there is no more basic tool than a shovel. Brian A. Cressy, founder and managing partner of Green Horizon Landscaping in Hopkinton, N.H., agrees. “No matter what kind of job you are doing, you need round-pointed shovels,” he says.
Other tools on Cressy’s must-have list include a 3- to 4-foot grade rake for grading beds and lawns, pruners in different sizes, hand edgers to cut deep edges for beds and brooms. “I insist on keeping project sites clean and tidy at the end of every day, not just at the end of the job,” he says. “This is a standard of service that is important to us, and that makes brooms one of our basic hand tools.”
When to rent.
It can make sense in some cases to rent rather than buy some hand tools. For Green Horizon, that is trenchers for irrigation system installations because they tend to need them for short amounts of time on particular jobs. Castlewood also rents tillers.
Don’t forget about materials Castlewood Custom Landscape & Design in Littleton, Colo. buys in bulk for flagstone and three types of pavers they generally quote for design/build projects. “Buying multiple pallets is the only way to get the price down,” Reale says. “We stick with a preferred dealer. It does not pay to spread business around.” At Green Horizon Landscaping, the only pavers and flagstones kept in inventory are leftovers from previous projects. Before the start of the season, the company focuses bulk buying on screened top soil, bark mulch and stone dust for patio and walkway prep. “We try to shop local to support the local economy,” Cressy says. “New Hampshire is a state of small towns and villages. Businesses know one another. What goes around comes around in terms of referrals and projects.” |
Reale and Cressy have lessons to share from mistakes they have made in purchasing hand tools. “We made a mistake once buying cheap chainsaws,” Reale says. “They kicked back so much; they were accidents waiting to happen. Rather than risk injuries to our guys, we junked them.”
“Not naming names, but we have learned not to buy from big-box and chain hardware stores,” Cressy says. “Hand tools made for homeowners may cost less, but they do not last. You end up spending more replacing them."
The 30 wheelbarrows Castlewood needs every year are a constant problem. Bigger, commercial models are sturdier, but it takes two men to move them. Homeowner models, which cost about $130 each, are lighter but break down after three months. Reale says they have yet to find an answer for this problem.
Buy in bulk.
To get the best value in hand tools purchased for design/build projects, Cressy says that one-off purchases end up costing contractors. He recommends bulk buying before the start of the season based on a tool inventory as the way to get the best price.
Before buying, there is no substitute for doing your homework. “Take the time to investigate,” he says. “Do not go for cheap. Look for value based on durability.”
When it comes to controlling the costs of hand tools, incentives are the key. “During the season, they are responsible for reporting what gets broken.
“We call it ‘bringing back the corpse.’ At the end of the year, we inventory again. If the inventory checks out, and every tool is accounted for, they get a $500 bonus check. This cuts down on the perennial problem of tools getting left on sites.”
The author is freelance writer based in Minneapolis.
Get curated news on YOUR industry.
Enter your email to receive our newsletters.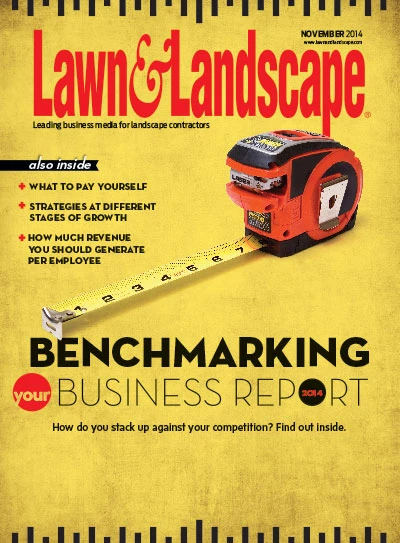
Explore the November 2014 Issue
Check out more from this issue and find your next story to read.
Latest from Lawn & Landscape
- Project EverGreen helps revitalize Milan Park in Detroit
- Trex Company wins Product of the Year, Judges’ Choice Winner at Environment+Energy Leader Awards
- General Equipment & Supplies in Fargo adds Takeuchi equipment
- Mariani Premier Group acquires Hazeltine Nurseries
- EnP Investments adds Mark McCarel as Northeast territory sales manager
- Our April issue is now live
- Ready or not
- Tribute to an industry guru