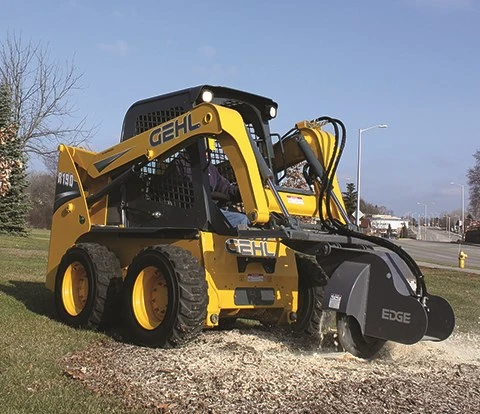
In an industry where the improper use of equipment can mean life or death, training never ends.
At both Mountain High Tree, Lawn & Landscape Co., and at Swingle Lawn, Tree & Landscape Care, training for new employees on the machines of their trade – wood chippers and grinders – begins day one. This includes start and stop procedures, and reading all warning labels and equipment manuals.
“OSHA standardizes the warning stickers on them so there are very specific points on the chipper explaining all these parts and pieces, and what their associated risks are,” says Nate Talocco, senior enhancement manager for Swingle, a Denver, Colo.-based company with $22 million in annual revenue and 250 employees.
That supervised operation may continue for several days or more, depending on the individual employee. At Swingle, employees are shown the equipment, then demonstrate its use and lastly show proficiency with operation. Talocco says one of the most common mistakes he sees operators make is moving too fast.
“Both types of equipment are designed to be safe when used properly and to aid in doing tree work, but people either get going before they completely understand how to properly use them,” he says.
“Also, using the equipment looks easy and I see folks just jump in before really getting a full training.”
Grinder operation is a little more complex they come in several different styles. Some are driven by hand or remote and the wide variety of complex controls make it a longer process to learn and become proficient, Talocco says. Attaining proficiency usually takes three months, he adds.
In conjunction with the initial training, employees are taught lock out procedures, according to Shane Tucker, trim production manager for Mountain High Tree, which is based in Lakewood, Co. The company employs close to 100 people and posts annual revenue totals $7.9 million. Mountain High provides primarily residential tree care including pruning, removal, stump grinding and plant care.
Employees at Mountain High Tree have a daily checklist they follow, which includes making sure all belts and chains have the proper tension, no welds on the machines are broken and that the machine is cleaned properly, he adds.
More than a dozen chippers are in operation at any given time between their two offices. A large wireless remote-controlled grinder is also used at a mulching facility.
Emergency controls are on the side of the mulching unit and employees are trained in manual operation of the controls so they can stop the machine in the case of emergency, Tucker says.
Never alone.
But Tucker and Talocco both stress employees at their businesses are never alone in the field. A supervisor or coworker may be called on to assist with the operation of these machines – even when the most veteran employees are behind the controls.
Having multiple employees on site also means if there is an emergency, someone can call 911 and give first aid. At Mountain High Tree, most crews are three-man, Tucker says.
“Our crews are very versatile,” he says. “They all can climb and do ground work.” At Swingle, it’s not uncommon to have three or four employees on one job.
“You really don’t need two people (from a profitability standpoint) but it’s a decision we made,” he says. “If there’s multiple stumps it works great because they can just follow behind and remove chips, fill in dirt and clean up.”
Precautions, training and group work are important, but the use and wear of proper safety equipment cannot be stressed enough, contractors say. Essential personal protective equipment for chippers and grinder operation includes hard hats, safety glasses and hearing protection, along with proper attire.
Constant reminders.
Training at these businesses includes staff updates with information from the manufacturer or through the Tree Care Industry Association. “You learn new things all the time. They (TCIA) come out with new standards for safety all the time so it’s always changing,” Tucker says. “It’s usually because an accident has happened, so they add a safety standard to make sure an accident doesn’t happen again.”
At Mountain High Tree, weekly safety meetings also typically include a topic for discussion. Chippers and grinders are addressed twice a year, Tucker says.
At Swingle, safety meetings also occur weekly, along with quarterly chipper training. Employees there are also encouraged to pursue Chipper Operator Specialist certification from TCIA, Talocco says.
Open communication.
“Never be too proud to ask questions,” Tucker says. Employees are trained to be aware of their surroundings and watch out for each other.
“We want to make them feel very comfortable doing tree work. It’s all about confidence and knowing your job. That’s what makes everyone go home safe at the end of the day,” Tucker says.
“Chippers are unforgiving. They don’t stop working, especially if they get a hold of a body part or limb.” Employees both new and old need to be reminded of safety procedures, Talocco adds.
“You either have power users who use it all the time and overlook the simple things, or you have people who don’t use it very often and they can forget the simple things because they don’t have practice,” he says.
The author is a freelancer based in Cleveland.
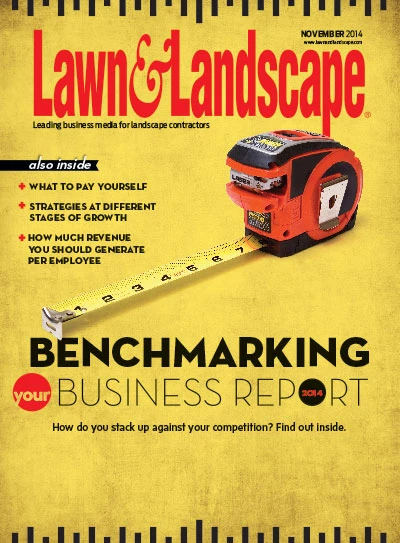
Explore the November 2014 Issue
Check out more from this issue and find your next story to read.
Latest from Lawn & Landscape
- Aphix acquires Curb Appeal Landscaping in Birmingham
- Project EverGreen helps revitalize Milan Park in Detroit
- Trex Company wins Product of the Year, Judges’ Choice Winner at Environment+Energy Leader Awards
- General Equipment & Supplies in Fargo adds Takeuchi equipment
- Mariani Premier Group acquires Hazeltine Nurseries
- EnP Investments adds Mark McCarel as Northeast territory sales manager
- Our April issue is now live
- Ready or not