It can turn a successful day of incident-free mowing into an instant nightmare: A zero-turn mower overturns on an embankment, pinning the operator upside down. Without the proper rollover protection system, the mower’s weight could crush the landscape contractor.
Whether the potentially survivable accident is made worse by a lack of safety equipment or operator fatigue, the end result can be disastrous. For instance, tragedy occurred in 2003 to a 42-year-old contractor in Greensboro, N.C., who was crushed by his overturned zero-turn. A year later, a 57-year-old contractor in Illinois died after he was knocked unconscious by a zero-turn that tipped over from a tire slipping on a drainage pipe. In 2005 and this January, two Florida contractors were mowing steep inclines when their mowers overturned in ponds. Both men drowned.
“These are some examples of people doing routine landscape work and they lost their lives doing it,” says Tony James, an executive with CNA Insurance, of Chicago, Ill. James suggests there are some simple safety measures contractors could follow daily that could enable them to work more safely.
For instance, mowing on shifty or hilly terrain can be done accident-free through a combination of operator know-how and safety equipment, but equipment alone shouldn’t lull anyone into a false sense of security, experts say. “There is no substitute for good judgment on the part of the equipment operator,” says R.A. Stucky, of Moundridge, Kan.-based Grasshopper. “If there is any uncertainty about the safety of mowing in a particular area or on a slope, don’t attempt to operate there.”
ROPS TO THE RESCUE. The biggest single safety development in recent years has been the standardization of Rollover Protection Systems (ROPS), says John Cloutier of Beatrice, Neb.-based Exmark. Used in conjunction with a seat belt, ROPS won’t prevent a mower from overturning, but can protect the operator from serious crushing injuries or death.
The system works like this: A stationary or foldable rollbar helps protect the operator if a zero-turn mower overturns. But an important and often-overlooked part of the system is the safety belt. If it’s not used, the system won’t work. “When the ROPS is up, should it roll, the operator is in a safety zone,” says Roy Dust, product specialist for Munsville, N.Y.-based Ferris. “But he’s only in a safety zone if that safety belt is used. Otherwise, he could be pinned in a rollover.” Experts caution that the use of ROPS should by no means give operators the feeling they can take risks or mow in hazardous conditions.
ROPS is offered as standard equipment on most new models of zero-turns. Many manufacturers offer both fixed and foldable ROPS systems, while others offer retrofitting kits for older mower models.
Manufacturers rely on a combination of safety standards, such as those from the American National Standards Institute (ANSI) and additional safety elements based on historical experiences when designing systems such as ROPS.
Systems like ROPS should always be utilized, but it’s not a magic wand, Stucky says. “ROPS is a precaution that contractors want to have in place; they don’t want the responsibility of not providing it to their operators. But don’t let ROPS provide a false sense of security in hazardous areas,” she says. “All these standard features combined with the good judgment of the operator contribute to safe operation of the mower.”
A ROPS system can add between $600 to $1,000 per mower, with $750 being the average, Dust says, adding that price shouldn’t be an issue concerning safety. “I think ROPS is a must-have,” Dust says. “Even if you’re mowing on a flat area, there’s always going to be a slope. It doesn’t have to be that high to have a rollover. I consider ROPS to be mandatory equipment.”
Because the rollover bar sits higher than the user, in some instances it could become entangled in low-hanging tree limbs or brush. But experts say those situations should never be a determinant not to utilize ROPS.
“There are applications where the vertical profile of the ROPS can result in snagging on limbs or prevent access onto an enclosed trailer,” Cloutier says. “However, this fairly infrequent mowing condition is a small price to pay should your machine roll over.”
When equipped with foldable ROPS, only fold down the ROPS to pass through storage doors or to pass into enclosed trailers, Stucky cautions.
Aside from the obvious injuries or deaths that can occur from rollovers, utilizing safety equipment such as ROPS is just good business. An accident such as a rollover can easily cost from thousands into the millions in worker’s compensation claims and increased liability insurance premiums, depending on the severity. “Consider the cost if a rollover occurred and the mower was not equipped with ROPS and seat belt, or equipped with a folded ROPS that was not deployed,” Stucky says. “It shouldn’t be an option to go without.”
Other safety features that have become standard and most desired by contractors include a hinged discharge shield that can be raised or will bend to pass through narrow openings and return to mowing position immediately; an ergonomic cushioned high-back seat with padded armrests and a seat switch that shuts off the engine when the operator leaves the seat without placing the levers in neutral position; and a disengagable PTO drive, Stucky says.
The seat switch is an indispensable addition to a mower, Dust says. “The biggest advantage is for someone who gets off of the seat to pick up something and accidentally slides their foot underneath the deck while getting back on,” he says. A seat switch adds only about $100 to the cost of the mower, he says. The only disadvantage could be having a seat switch that doesn’t account for the weight of the rider, Dust says. In some instances, a lighter operator could hit bumps and come out of the seat just enough to start and stop the mower blades several times. Seat switches have become more accurate in recent years, he adds.
A well-padded ergonomic seat will pay big dividends to the operator. “When someone’s on a machine for an extended period of time, a quality seat is well worth the cost,” Dust says. “Although a good seat might add $400 to $700 to the cost of the mower, operators really appreciate a quality seat.”
PRECAUTIONS ON ZERO-TURNS. With the nimble nature and potential speed of a zero-turn, an operator can sometimes forget the inherent dangers of this useful machine. And when contractors spend an average of $9,976 on riding mowers each year, according to Lawn & Landscape research, protecting this investment with proper practices is crucial.
Common sense should apply when deciding not to use a zero-turn due to the conditions. Cloutier suggests a few rules of thumb to avoid the most common accidents that result in injuries on hilly terrain.
- A hillside that exceeds the recommended degree of gradient should always be mowed with a walk-behind or a mower that was specifically designed for extreme gradient mowing applications.
- A zero-turn should never be used on a slope greater than 15 degrees. To check a slope in doubt, the operator should attempt to back up to the slope with the cutter deck down, according to Mayville, Wis.-based Scag. If the zero-turn can’t back up without the wheels slipping, avoid cutting the slope with the machine.
- Avoid hillside mowing with heavy moisture after recent rainfall or wetness as a result of morning dew. Properties that operators have mowed for years take on an entirely different feel and risk factor as a result of precipitation on the grass. Contractors should plan their day so that hilly properties have an opportunity to dry out, Cloutier says. If contractors have no choice but to mow early, he suggests utilizing walk-behinds.
- Mowing around the perimeter of waterways and retention ponds or retaining walls requires extreme caution. Always leave at least two cutting paths to the edge of these hazards.
If a zero-turn simply isn’t practical due to the slope, a walk-behind mower might be a better choice. Operators should use walk-behinds across the slope, as opposed to up and down the slope for zero-turns. Going across the slope can reduce injuries to hands and feet should the operator fall. If a landscape contractor falls using a walk-behind uphill, for example, the mower could roll back and injure him, even if the control bar is let go. Mowing up and down a slope using a zero-turn can help avoid tipping.
PUTTING SAFETY TO WORK. It’s easy to focus on just the machine and forget how the operator is an integral part of the overall safety picture. Some basic precautions can put the contractor on the path to a safe day on the job. Loose-fitting clothes, for example, are a safety hazard. All clothing should be snug and shirt-tails should be tucked in and long hair should be tied into a ponytail and tucked under the shirt, industry experts say.
Fatigue is another issue that plagues daily mower operators. But a zero-turn riding mower itself can instill safer operation in the first place. “Using a rider for all-day mowing will eliminate operator fatigue from excessive walking, and eliminate knee and joint stress injuries,” Stucky says. “An ergonomic zero-turn mower not only enhances the operator’s quality of life but helps avoid accidents that can occur with poor judgment induced by fatigue.”
It’s also important for the contractor to walk the grounds to be mowed to ensure there are no rocks, sticks or other foreign objects that could be thrown by the blades. Tall, overgrown vegetation and rough or unfamiliar terrain is better maintained with a hand-held string trimmer, walk-behind mower, four-wheel drive or slope mower, Stucky says. And contractors should discuss with clients that planting vegetation that does not require mowing is often the best solution for problem areas.
Safety measures are important not just for landscape contractors, but bystanders near the work site, as well. Contractors work on uncontrolled job sites where people just passing through could be injured by errant rocks or sticks struck by a blade. “Operating with a commitment to mower safety frees employees to do their best work, and avoids the pitfalls of dealing with accidents or property damage which take away from the desired outcome of a job well done and a happy customer,” Stucky says. “Accidents are costly to those involved and to the company as a whole.”
The best-laid plans for mowing can go awry if the machine isn’t properly maintained. Basic maintenance can cause potentially catastrophic accidents. Improper tire pressure, for example, can cause a loss of traction, which could cause a rollover on hilly terrain. One easy way to remember safety tips is to review the safety decals on the machine before beginning operation each day, Stucky says.
“Your mower is a tool that is very safe in design when used as suggested, however you cannot lose your attention and focus,” Cloutier says. “Construction workers use rotary saws all day everyday but put their safety at risk by taking their tool for granted. Operators of mowers should always understand the tool they are utilizing and not let their guard down.”
Beyond simply forgetting safety basics, contractors can get into trouble by ignoring safety features. Bypassing safety switches, such as operator presence detectors or removing protective devices such as ROPS, seat belts or discharge deflectors can lead to injury or damage to property. “Operators should be taught and expected to take responsibility for seeing that all safety shields and devices are properly installed before operation,” Stucky says. Follow all warning decals and instructions in the operator’s manual. These are designed and intended to remind operators of safe operation and warn them of potential hazards or dangers of power equipment.”
Stucky suggests machines be assigned to one operator. “When he’s familiar with the machine he will be able to operate more safely by understanding the ins and outs of how the machine operates and by taking responsibility for proper operation and maintenance,” she says.
Cloutier suggests operational and safety programs. A study by the Construction Industry Workforce Foundation shows programs of this kind pay off handsomely. For each dollar spent on safety training, firms get $2 in return, not to mention a 17 percent increase in productivity and 19 percent reduction in turnover and absenteeism.
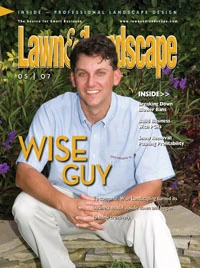
Explore the May 2007 Issue
Check out more from this issue and find your next story to read.
Latest from Lawn & Landscape
- Coxreels expands V-100 Series product line
- Landscape Workshop expands with 2 acquisitions
- Wilson360 adds Daniel Grange as new consultant
- Batman and business
- CH Products releases new tree stabilizer
- Savannah Bananas founder Jesse Cole to speak at Equip Exposition
- Catch up on last year's Benchmarking report
- Davey Tree promotes Kevin Marks as VP of Western operations