
Safety is no accident. Landscape firms committed to reducing risk and preparing employees to mitigate accidents in the field understand that keeping a clean record takes work. This month, Lawn & Landscape spoke with three companies about their safety training and systems to learn how they protect their people, equipment and properties.
Always aware
Training at Keep It Green Landscaping is a lot like teaching employees to ride a bike. “First you hold the back of the seat, then you run alongside of them before they go off on their own,” says Dyle MacGregor, president of the Fair Lawn, New Jersey-based company.
A human touch to training makes all the difference, MacGregor says. Safety classes and video instruction provide a foundation for learning safe equipment operation, but you don’t really “get it” until you use tools in the field. And complacency is safety’s worst enemy.
That’s why MacGregor makes sure to deliver the “play it safe” message in a variety of ways, including classes sponsored by manufacturers, quick tailgate meetings, sharing articles and relating personal stories.
"There’s no room for error with safety. The first time you don’t take it seriously could be your last." Dyle MacGregor, Keep It Green Landscaping
“You have to stay vigilant,” he says. “You have to put a spin on (safety) because after a while, it’s like the Charlie Brown ‘wahh-wahh-wahh’ so we present it in different ways even though it’s the exact same message to stay safe.”
Experiences can be a real eye-opener for workers and they don’t have to be your own, MacGregor says. Another landscaper shared a story with him that illustrated the real danger that can result from improper operation of seemingly simple equipment like string trimmers.
The story is about a worker who was not wearing safety glasses when a small rock kicked up. “He actually lost his eye and is blind in that eye,” MacGregor says. “The worst part is that the worker still does not wear safety glasses.”

Relating that experience to his people reminds them that accidents do happen, and basic equipment is in fact capable of causing lifelong injury.
Reminding employees on jobsites about the importance of safety is critical to keeping the message in front of employees at all times.
If MacGregor catches a technician operating equipment without the required personal protective equipment, he might make a remark like: “Are eyes on sale at Target this week? Where are you going to get your new ears?” There’s zero tolerance at Keep It Green for neglecting eye and ear protection.
Every paycheck employees get also includes a safety tip sheet. The notices are triple punched so crewmembers can insert them into their company handbook. “Every once in a while, we’ll review one of those sheets as a group,” MacGregor says.
MacGregor is careful to time safety lessons with what’s going on in the field. “If it’s hot out, we’ll address heat exhaustion, and if we’re putting in 50 trees on a property we might talk about proper lifting,” he says.
Teaching by example goes back to the whole riding a bike example. “We might actually put items on the ground and say, ‘Lift this up,’ and we’ll critique each other,” MacGregor says, adding that crewmembers practice the safe use of riding equipment on site.
“The first time you don’t take it seriously could be your last. You can’t be lulled into the idea that you’ve done your job for 20 years so you know everything about it. Always stay aware.”
A safety culture
“We want everyone to go home from work in the same condition they were when they got here in the morning,” says Abby Santos, co-owner of No Ka Oi Landscaping on Kauai, Hawaii.
The goal sounds simple enough, but executing it takes diligence and a commitment to sending the message of safety to crewmembers in the field. No Ka Oi has been recognized for its dedication to safety by earning Safety Recognition Awards from the National Association of Landscape Professionals (formerly PLANET), including the Best of the Best award, which the company has received since 2011.

“In order to get that award, you have to be accident-free for the three prior years, so really we’ve had seven years of no incidents,” Santos says, adding that No Ka Oi is into another completely safe season. And on Kauai, the season is year-round.
“Safety starts from the beginning, and it has to be part of the culture,” Santos says. Employees all receive personal protective equipment and the company reissues safety glasses and earplugs on a monthly basis.
“We visit sites and bring ear plugs, safety glasses and gloves for whoever needs them,” she says.“We want them to know that it’s important to us that they’re safe and their equipment is working properly.”
"They’re out there on the front lines, and you can talk about safety as much as you want, but they have to know we follow through." Abby Santos, No Ka Oi Landscaping
Employees are expected to report if there are problems with equipment. Meanwhile, a staff mechanic travels to the various commercial and resort sites No Ka Oi services. “He makes sure their equipment is running properly and does safety checks,” she says.
Also, No Ka Oi is working with its workers’ compensation provider to conduct on-site inspections – the consultant will visit construction and maintenance sites – and an office safety audit. The service is free, and shows employees that the company walks the safety walk instead of just talking the talk.
Santos points out that providing a safe working environment includes No Ka Oi’s home base where the provider will look for any Occupational Safety and Health Administration violations.
It may sound like little stuff, but No Ka Oi underwent an OSHA inspection years ago and while the company didn’t get fined, there were some minor corrections it had to make like fixing a frayed plug on a piece of equipment.
Partnering with the workers’ compensation provider to emphasize safety in and out of the office underscores the safety message to No Ka Oi’s people and clients.
“Hotels and their guests need to know how important it is for us to take care of equipment and that we don’t want anyone to get injured,” Santos says, adding that crewmembers are working on properties while visitors are outside, too. “We want our clients to know that No Ka Oi is protecting them and their customers. We are very cautious.”
The work No Ka Oi performs can sometimes pose risks, such as trimming coconut palm trees. “We value our climbers and make sure they have the proper equipment, including hard hats and (quality) rope,” she says.
Now, more clients are asking questions about safety data sheets (formerly material safety data sheets). “We can assure them that we have the official documents in a binder and produce the information they need,” Santos says.
Upholding a reputation for being a safe company means never letting one’s guard down and continuing to train and find new ways of keeping crewmembers accountable.
For example, No Ka Oi foremen use a safety training app called Safety Meeting App to track safety meeting topics. “They ‘check in’ their whole crew for safety meetings, and they complete one of the safety meetings,” Santos says.
Back at the office, the administrative team can view safety meeting progress online. “We can make sure that everyone has completed (the module),” Santos says.
“These tools let everyone in the company know that safety is important to us,” Santos says. “They’re out there on the front lines, and you can talk about safety as much as you want, but they have to know we follow through.”
‘High’ risk
The visual is grisly, but the statement is a fact. “A chainsaw doesn’t know the difference between wood and flesh,” says Bryan Buero, owner of Trio Outdoor Maintenance in Mount Clemens, Michigan.
“The chainsaw does what the operator lets it do, so it’s critical to develop the skill and make sure you know how to react.”
Buero says it was one incident that triggered ArborMaster certification – an organization focused on education and training for professionals working with, in and around trees.
Buero and another crewmember were removing a branch on a 50-foot maple tree that was hanging over a client’s house. The weather was nice, and the rigging was properly put in place for the job.
"You can have meetings all day, but people will only retain so much." Bryan Buero, Trio Outdoor Maintenance
“But when we cut the branch, the wind grabbed it and took it the opposite direction,” Buero says, adding that a light breeze can be a real game changer at higher heights.
“No one got hurt, but neither of us was expecting that to happen. After that I said, ‘OK, it’s time to get trained.’”
ArborMaster training is one of the best safety steps Buero has taken for himself and employees, he says of earning the certification in 2004. “When you train someone, you don’t know how they will react under pressure,” he says.
Buero had plenty of experience with trees, but the additional training cemented his skills and safety awareness.
“You never know what is going to happen because wood has a mind of its own,” Buero says.
He and his crew hold tailgate meetings on a daily basis. “Each job has different risks,” he says.
Buero ultimately wants to teach his crewmembers critical thinking.
“A chainsaw doesn’t know the difference between wood and flesh.” Bryan Buero, Trio Outdoor Maintenance
“I’ll get workers who say, ‘I’ve done this for years,’ and I’ll say, ‘Yeah, that means you have experience but you don’t know how we do it.’”
In fact, re-training a seasoned landscaper can be more difficult than teaching a newbie how to use equipment from scratch.
Tree jobs at Trio Outdoor Maintenance involve tools including chainsaws, chippers, grinders, ropes and a bucket truck. Safety equipment includes eye and ear protection, gloves, chaps, safety vests and hard hats.
When a new employee comes on board, they shadow a longtime team member or Buero.
Then, after some practice, the crewmember can gradually take on tasks. Everyone watches out for each other.
“Everyone trains everyone,” Buero says.
“There is no room for anyone to fall because there is always someone watching what you are doing.”
Buero wants his people to always be thinking: What if?
“If you’re in the middle of cutting a branch, it’s too late,” he says of mitigating risk and making safe decisions in the field. “I teach them the what-ifs before problems happen, and that’s where that critical thinking comes in.”
Buero uses a variety of learning tools. He clips articles from magazines to share and he shows the team videos. They spend time together in the field problem-solving before jobs.
He’s careful to distill information and leave employees with a few key takeaways. “You can have meetings all day, but people will only retain so much,” he says.
Get curated news on YOUR industry.
Enter your email to receive our newsletters.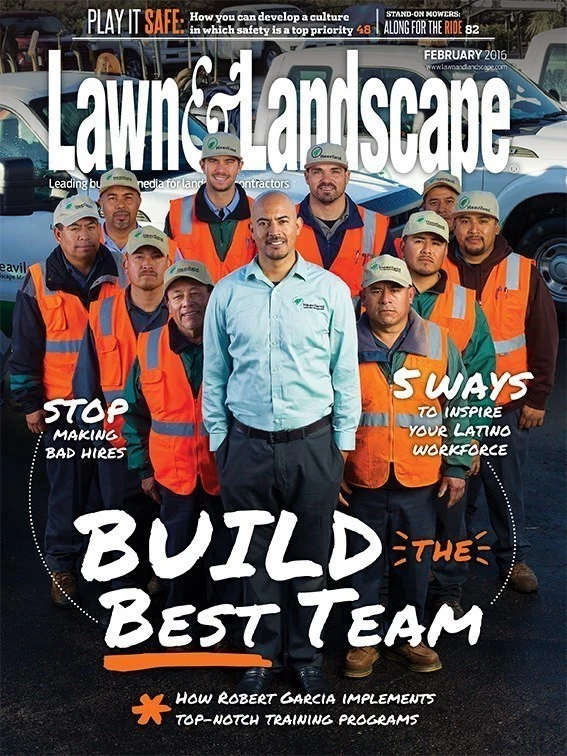
Explore the February 2016 Issue
Check out more from this issue and find your next story to read.
Latest from Lawn & Landscape
- Senske Family of Companies acquires Huron Pest Control
- Sunseeker unveils new X7 Series Robotic Mowers
- Bobcat Company debuts MT120 mini track loader
- Senske Family of Companies opens new corporate office
- Autonomowus Lawn Company adds robotic mowers to Genan tire recycling plant
- Visterra Landscape Group acquires Cleveland-based H&M Landscaping
- SiteOne names Carrothers VP of agronomic business development
- Batman and business