Just as cutting and clean-up comprise a landscape contractor’s daily to-do list, considering potential equipment hazards is an obligation equipment operators can’t afford to ignore. The stakes are high for those mindlessly operating commercial mowers - negligent equipment use can injure the technician as well as bystanders and their vehicles, homes and properties.
For safety’s sake, conscientious landscape contractors should add responsible mower use to their job description. “Safety is not above and beyond, it is part of the job and part of why you are getting paid,” stressed Lou Kobus, agronomist and CEO, Village Turf, Mt. Vernon, Va.
HIGH-RISK HAZARDS. Visibility, noise, thrown objects, speed, comfort-these concerns and others form a lengthy list of areas that demand attention to avoid dangerous outcomes.
“There is a relationship between sound for the operator’s hearing and for his ability to be aware of what’s going on around him,” noted Gregg Breningmeyer, marketing manager, commercial mowing, John Deere Worldwide Commercial Consumer Equipment Division, Raleigh, N.C. “Operator comfort in an indirect way has a lot to do with safety, because as operators become fatigued, they are less aware and tend to be less careful.”
Bill Shea, vice president of sales, Ferris Industries, Munnsville, N.Y., said operator fatigue is the most common cause of mower-related injuries as most technicians work long hours. “By the end of the day, employees might not be following the safety procedures that they are supposed to follow,” he said. “As time goes on, everyone gets a little sloppy, and technicians can walk a lot of miles during the day with walk-behinds.”
Speed is also a safety and quality issue, Breningmeyer added, noting that mowers that exceed 10 to 12 miles per hour might not to process the volume of clippings through the deck, which decreases the quality of the cut. Also, mowers that move too quickly might fail braking tests.
Tip speed - or speed of the mower blade - also is a common inadequacy in the industry, added Mike Mack, vice president for marketing and sales, John Deere. “A good deck design can control the tip speed with the discharge shoot,” he explained.
Mowers that fail a ball-bearing test most likely exceed the ANSI standard of 19,000 revolutions per minute, create more noise, generate a detrimental velocity through the blade tip and increase the risk of shattering a blade, Breningmeyer noted.
Beyond spinning blades, outside considerations - the neighbors, for example - also figure into the risk factor list, noted Mark Meagher, marketing manager, Dixie Chopper, Coatesville, Ind.
“You need to have your wits about you while you’re mowing,” he added. “Someone on a riding mower might think you can just go out and drive around the yard, but there are other things you need to worry about - houses, trees, hillsides, your safety and that of others, as far as other people within an area of flying debris.”
Risk Reducers |
“Insurance companies are becoming very selective about which risks they want to take on,” noted Peter Ruvalcaba, loss control, CNA Commercial Insurance, Chicago, Ill. “This evidence is visible to your insurance company, your employees and their families, OSHA and your customers.” The following are signs that a landscape company is committed to a safety program and is in a favorable position for better insurance rates, Ruvalcaba listed. |
Peter Ruvalcaba, loss control, CNA Insurance, Chicago, Ill., reported that nearly 40 percent of “struck claims,” claims due to an employee being struck by objects including the mower body, blade or something ejected from the discharge shoot, are caused by equipment contractors use, including mowers. These injuries are reduced when technicians mow during off-hours, when there are not as many bystanders present, and when operators position the discharge shoot toward the property and never toward the sidewalk, cars or people, he said.
“Bad things only happen when the engine is running,” Meagher commented, which is why respecting a mower’s safety devices and not overriding an automatic engine shut-off function is critical to minimizing on-the-job risks. Most commercial mowers are equipped with a function that allows the engine to continue running but stops blade rotation when an operator dismounts the machine or lets go of the controls on a walk-behind mower. Some offer a device that cuts the engine completely.
Roll-over protection systems (ROPS) are also available on some commercial mowers and can prevent serious injuries caused by mowers that tip over, Mack added.
However, operators must properly utilize safety features and respect shut-off functions in order for them to dependably reduce danger. Meagher categorized most mower accidents in two categories: Operator carelessness and safety device negligence. Ultimately, the technician is responsible for making sound judgment calls while operating equipment. “Safety is an attitude and it starts with you,” he reminded. “You have to be in a safety state of mind.”
SAFETY-MINDED SUGGESTIONS. Beyond mechanisms, safety is a matter of judgment and responsibility. However, Kobus pointed out that “common sense is not always common - you have to teach people what is good and what is bad, especially with problem mowing areas,” he explained.
While Kobus admitted there are endless possible pitfalls that can put a damper on even a detailed safety program, the odds taper when contractors stress precautions. “A thousand things could go wrong, but the chances are diminished with a well-maintained machine and a good operator,” he said.
Kobus assigns responsibility to his technicians - each employee maintains and operates a designated mower. He claimed that holding workers accountable for maintenance reduces accidents.
“Each technician is responsible for a machine,” he explained. “In the morning, they check the oil, gas and go over the entire machine. At night, machines get cleaned, blades changed and the mower is topped off with fuel.
“When you run a maintenance check like that, your safety is a lot more assured,” he stressed. “If they are conscientious enough to take care of their mower, then they’ll take care of the truck, trailers and other equipment - it’s infectious.”
In order for Kobus’ employees to assume responsibility for their mowers, novices must learn maintenance and operation methods, he said. Progressive training -advancing from edgers to blowers to riding mowers - provides employees detailed instructions.
By emphasizing the importance of mower safety, companies reduce the probability of work-related injuries no matter the size of the staff, said Andy Maushbaugh, loss control engineering manager, FMI, Edwardsville, Ill. “The company safety program with tailgate safety meetings are a must - maybe 10 minutes at the start of the day to get operators ready,” he said. “Give employees one topic to take out into the field to bring safety to the forefront.”
For some employees, hazards become more real when they see injuries caused by negligent mower use, Mack noted. One John Deere engineer kept a picture book of accident victims to show to employees. “We try to visualize safety on a personal level instead of a statistical level,” he emphasized.
Personal responsibility for safety includes not only training and maintenance, but also wearing protective equipment such as long-sleeved shirts, sturdy work boots with slip-resistant soles, safety glasses, hearing protection and leather gloves when working around cutting and puncture hazards, Ruvalcaba listed.
Finally, to avoid accidents that spring from haphazard mowing, contractors should press safety as a priority over time. In an industry where productivity means profit, technicians might speed through a job, leaving safety concerns at the curb, Breningmeyer noted.
“There are a number of small operators that knowingly take risks every day because of the pressure of productivity,” he commented. “The way to compete in the marketplace in the minds of some of these folks is to do the job faster. When that happens you have a dangerous situation.”
COMPENSATION FOR CARE. Since safety must be practiced full-time, many business owners offer incentives to encourage employees to practice maintenance, protection and sound judgment and to remind staff that safety is a constant function of their job.
Ruvalcaba described a reward program at one company where employees who work without a lost time injury are rewarded with $25 gift certificates. If no lost time injuries occur during the calendar year, five employees’ names are drawn from a hat and awarded a $1,000 prize, he explained.
“The prizes are awarded at the company Christmas party,” he added. “What better time to celebrate - and celebrate safely - that no one was seriously injured that year.”
Meagher stressed that safety goes beyond personal injury. “You think of a safe day as one without bodily injury, but a safe day might be a day where you don’t hurt others or put a scratch on someone’s vehicle with debris,” he described.
Company compensation for implementing safety programs can payoff on the insurance end, as many insurance agencies offer credits for safety initiatives, Maushbaugh noted.
“One serious accident can drive a company’s experience modification into the debit area, and that will hang around for three years,” Maushbaugh added. “Companies relive accidents as they pay for years, and injured employees will be reliving them for a lifetime.”
The bottom line is, “safety pays,” he stressed.
Since insurance pricing is based on the quality of the risk a company represents, a contractor who implements controls to prevent and reduce losses is in the position to receive a better insurance rate than a company that doesn’t do so, Ruvalcaba added. (See Risk Reducers sidebar above.)
When management sets a safety example and establishes a program, the technician and company both will reap the rewards.
“Safety has to be prominent in our minds,” Meagher emphasized. “Safety is as safety does. It truly is an attitude. You have to think as you’re mowing and you have to be aware of other people’s properties. You have to be safety conscious.”
The author is the Assistant Editor of Lawn & Landscape magazine.
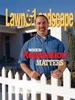
Explore the January 2001 Issue
Check out more from this issue and find your next story to read.
Latest from Lawn & Landscape
- Wilson360 adds Daniel Grange as new consultant
- Batman and business
- CH Products releases new tree stabilizer
- Savannah Bananas founder Jesse Cole to speak at Equip Exposition
- Catch up on last year's Benchmarking report
- Davey Tree promotes Kevin Marks as VP of Western operations
- Bobcat Company names 2025 Dealer Leadership Groups
- Green Lawn Fertilizing/Green Pest Solutions awards employee new truck for safe driving